金牌会员
已认?/p>
在现有技术中,测量软包电芯平整度的方法主要是肉眼观察法、千分尺测厚或激光扫描法。肉眼观察法即我们俗称的目测法,就是利用可见光观察电芯的表面状态,是一种粗糙的不可定量的观察方法,利用可见光观察虽然快捷,但是无法定量的给出电芯的平整度的差异。激光扫描法是利用光学设备,将电芯的整个轮廓扫描后制作成3D模型,然后计算整体的厚度值与断面的厚度值的差值,虽然可以定量测量,但是设备昂贵,应用有限¹。也有研究人员通过仿真模拟了模组电芯的表面力分布mapping,也可看出明显的压力分布不均的现象,这一方面与电芯初始的平整度有关,另一方面也与后续充放电过程中电流密度分布不均导致的应力分布差异有关²。本文运用电芯压力分布系统(BPD1000)监控电芯不同位置的压力分布情况,从而快速量化评不同尺寸电芯的平整度、/p>
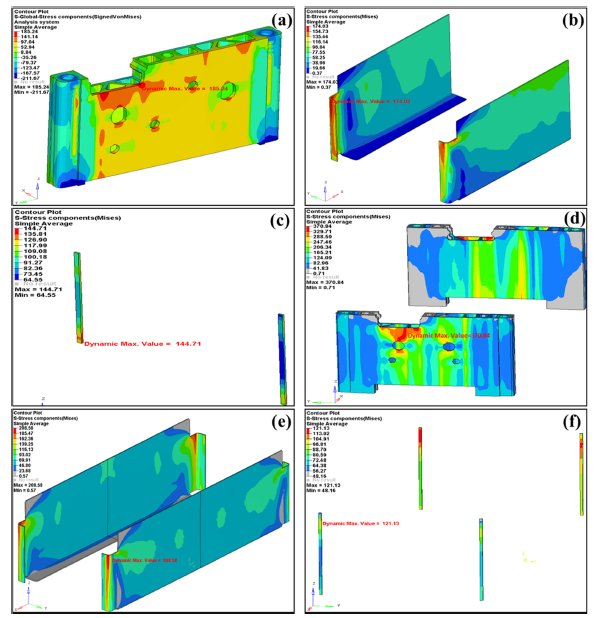
?. 仿真模拟模组电池的应力分布±/span>
实验设备与测试方泔/strong>
1.测试设备:原位膨胀测试系统SWE2110,电芯压力分布系统,型号BPD1000(IEST元能科技),可施加最大压强约?.8MPa、/p>
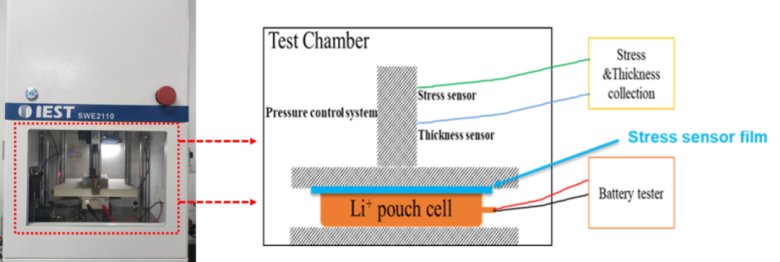
?. 电芯压力分布测试示意国/span>
2.测试参数9/strong>
2.1 电芯信息如表1所示、/p>
?. 电芯信息
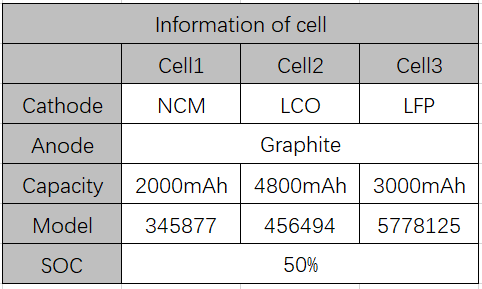
2.2 测试流程:将电芯置于原位膨胀分析?SWE2110)测试腔中,同时把压力分布膜平铺于电芯表面,设置恒间隙模式,调节恒间隙压?00kg(即给电芯施?00kg外力? 开启压力分布系统(BPD1000)采集并显示电芯表面压力分布数据、/p>
结果分析
使用压力分布系统(BPD1000)分别测试如下三款电芯压力分布情况,?.5*9.5mm 划分成各个小区域,并用色阶显示电芯各区域受力情况,结果如?所示:三款电芯都受力分布都不一致,若把各个区域受力算术和,会发现总力会小?00kg,这主要是由于各个薄膜传感器排布时之间存在间隙,并且间隙处压力未统计有关、/p>
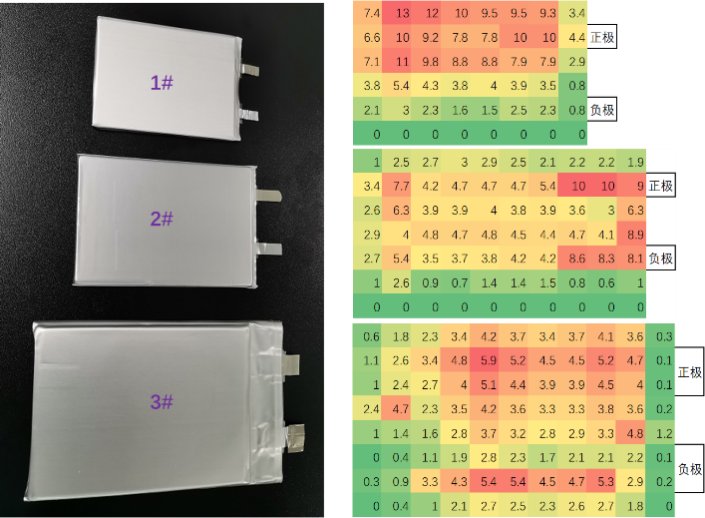
?. 电芯充放电电压和压力变化曲线
进一步分析电芯表面不同位置的平整度原因,如图4所示,3#电芯头尾部压力是因为铝箔冲坑尺寸较极片有较大的余量,头尾部下陷无压力,另外有贴收尾胶纸的位置,都表现出较大的压力,这很可能是导致其不平整的重要因素之一、/p>
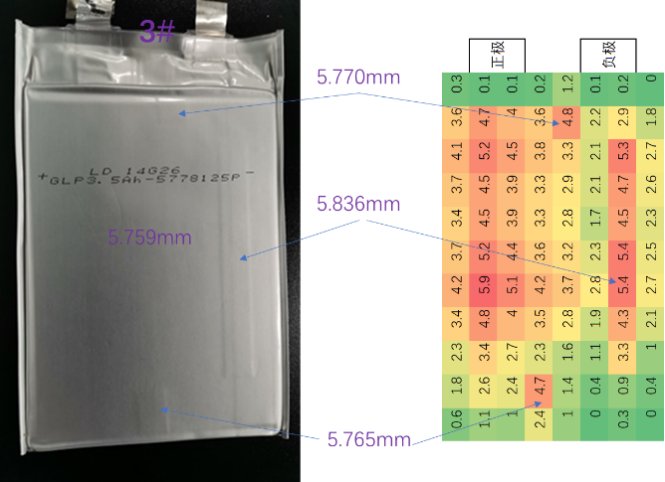
?. 3#电芯压力分布与实物对?/span>
分析2#电芯压力分布情况如图5所示:可明显看出正负极极耳位置受力明显,并且边缘无贴胶纸位置基本不受力,因此极耳厚度规格和胶纸贴附很可能是影响2#电芯平整的重要因素之一、/p>
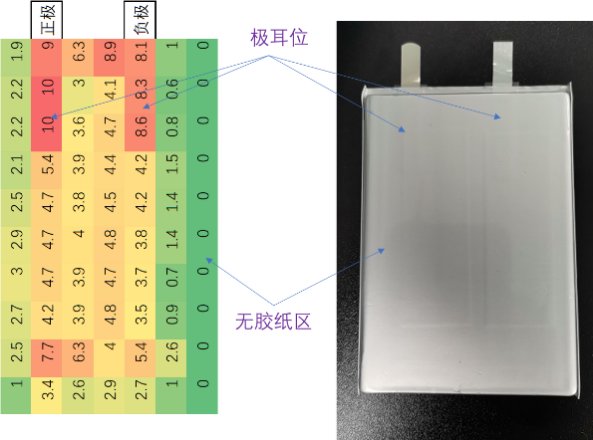
?. 2#电芯压力分布与实物对?/span>
对于1#电芯则并没有表现出与2#?#电芯类似的关联性,说明除了胶纸和极耳因素外,还有其它设计方面更深层次的因素。相关技术人员可以据此进行更深层次的分析、/p>
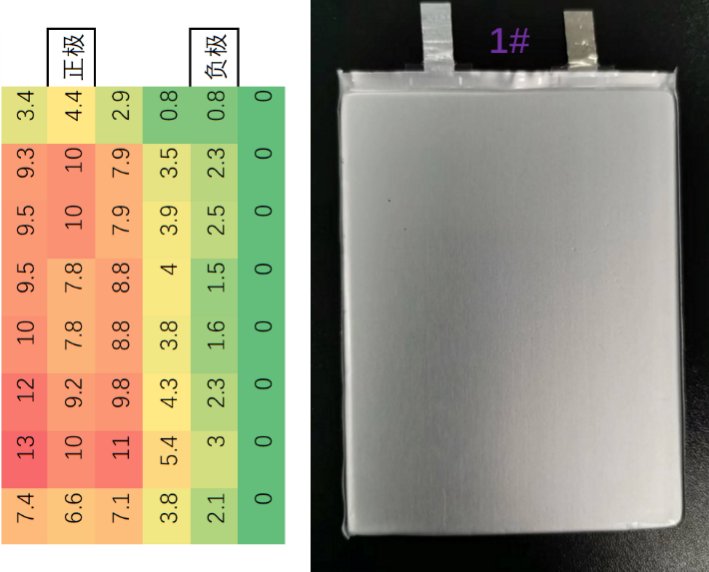
?. 1#电芯压力分布与实物对?/span>
设定初始压力300kg,在恒定间隙模式下测量电芯表面的压力情况。这种情况下,电芯厚度不均匀就会导致测试压力分布不均匀。电芯产生厚度或压力分布不均匀的原因主要包括:(1) 极片厚度不均匀性导致电芯不平整,一般正负极极片厚度?00-200μm,如果正负极极片厚度偏差大于5μm,正负极极片叠片数量?1片,则厚度偏差可以达?.2mm?2) 隔膜、铝塑膜等部件厚度不均匀导致电芯不平整;(3) 终止胶带会导致电芯不平整?4) 电芯叠片过程中,极片和隔膜叠合不紧密,存在的空隙导致的不平整。一般叠片之后电芯会进行热压平整形处理,热压整形可以使极片和隔膜叠合更紧密,降低空隙,从而降低电池内阻,同时也会提高电芯厚度的均匀性;(5) 电芯注液封口工艺过程中,真空度较低,封口抽真空不完全,铝塑膜内存在气体也会导致电芯厚度不均匀?6) 导电剂和粘结剂吸液后发生溶胀,会使电芯厚度增加,如果导电剂和粘结剂在极片内分布不均匀,也可能导致电芯厚度不均匀?7) 电解液在预充化成老化过程中发生分解,产生气体也可能导致电芯厚度不均匀、/p>
电芯厚度不均匀时,在充放电过程中会导致极片受到不同的铝塑膜外壳压力作用,可能导致充放电状态的不均匀性,降低电池的容量和稳定性。因此,电芯在设计和生产制造中需要控制平整度,提高电芯一致性。特别需要注意的工艺包括?1) 极片涂布和辊压厚度控制,提高厚度均匀性;(2) 合适的热压工艺提高厚度均匀性;(3) 铝塑膜冲壳和组装工艺确保电芯平整度;(4) 注液封口工艺确保去除内部空气和电解液的均匀性、/p>
总结
本文通过采用电芯压力分布系统(BPD1000)表征了三款不同体系电芯压力分布情况,从而表征电芯表面平整度。从结果分析电芯工艺设计与电芯压力分布(平整度)存在一定的关联性,技术人员可以通过压力分布系统制定合适的的分布标准,用于监控出货电芯批次稳定性、/p>
参考文?/strong>
1. 暴旭 任正 郑彦 马华 刘峰 王驰? 定量确定电芯平整度的方法 [P] . 中国:CN112665548B?022.5.
2.Yongkun Li, Chuang Wei, Yumao Sheng, Feipeng Jiao, and Kai Wu. Swelling Force in Lithium-Ion Power Batteries,Ind. Eng.Chem. Res?020, 59, 27, 12313?2318.