金牌会员
已认?/p>
言
随着传统能源的日益枯竭,锂离子电池凭借着循环寿命长、能量密度高等特性被广泛应用于消费电子、新能源汽车、光伏储能等领域,但是随之而来的安全问题也引起了用户的极大关注。锂离子电池在发生安全故障的早期往往会出现明显的膨胀形变,并造成电池之间的显著压力变化,而这种膨胀远早于温度异常和气体溢出现象。因此,研究锂离子电池的膨胀行为,总结造成锂离子电池形变的原因,对提高电池安全性及开发锂离子电池热失控预警系统具有重要的意义、/p>
一方面正负极材料在充放电过程中由于?嵌锂而导致结构发生一定的硬膨胀[1-3],另一方面锂离子电池在化成、循环老化、浮充、存储等工况下也会由于各种化学或电化学反应而产生气佒sup>[4-6],进而造成电芯鼓包,即发生了软膨胀行为。虽然二者表现形式类似,但形成机理却完全不同。锂离子电池在整个正常充放电循环中都会伴随着不同程度的产气膨胀,其中电解液分解是最主要的产气来源,一是由于电池内部的水分会与电解液反应并产生CO₂、H₂、O₂等气体;二是电解液中的EC、DEC等溶剂会与电极材料的副反应产物生成大量的自由基,再经过链式反应释放大量的烃类气体。而脱/嵌锂导致的硬膨胀在充放电循环中是可逆的,但是这种反复的膨胀与收缩也会累积内应力,并造成电极断裂等不可逆变形。通过区分硬膨胀和软膨胀,深入研究锂离子电池的膨胀机理与影响因素,可以更有针对性地对电池设计、制造和操作条件进行优化,并提供有价值的参考意义、/p>
本文选取市面上研究较多的Si/C负极,采用IEST元能科技的原位体积监控仪(GVM)并配合原位膨胀分析仪(SWE),有效地对NCM/SiC软包电池在化成过程中的软/硬膨胀行为进行定量分离,这对锂离子电池化成工艺的优化与改善具有显著的指导性意义、/p>
1. 实验设备与测试方泔/strong>
1.1 实验设备
?(a)原位产气体积监控仪,型号GVM2200;图1(b)原位膨胀分析仪,型号SWE2110、/p>
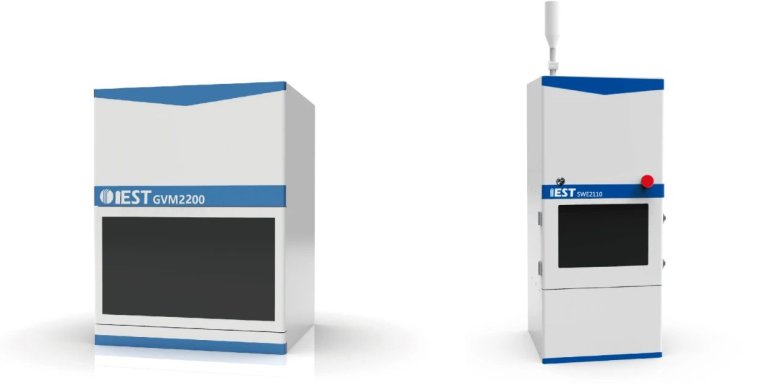
?(a) GVM2200设备外观图;?(b) SWE2110设备外观国/span>
1.2 测试信息及流稊/strong>
1.2.1电芯信息如表1所示:
?.测试电芯信息
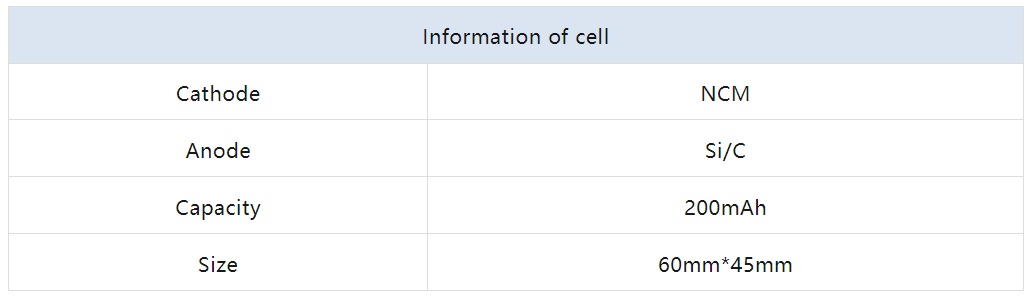
1.2.2化成充电流程9/p>
?.化成充电流程
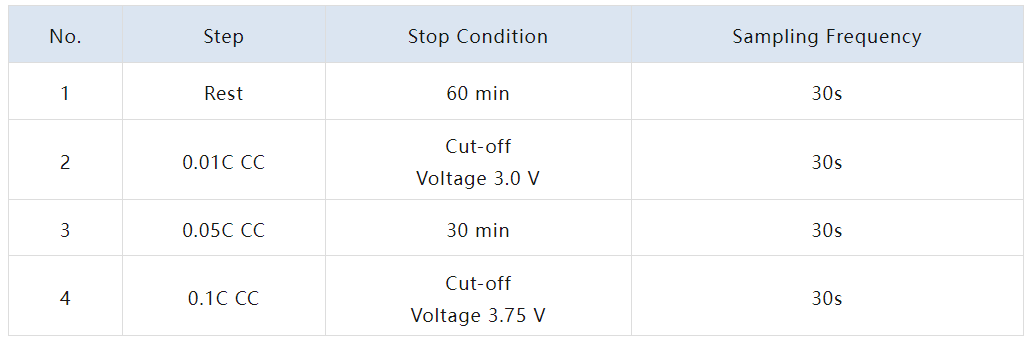
1.2.3实验流程9/p>
电芯膨胀体积测试9/strong>将待测电芯(带气袋)放入GVM2200对应通道,开启MISS软件,设置各通道对应的电芯编号和采样频率等参数,软件自动读取实时体积、测试温度、电流、电压、容量等数据、/p>
电芯膨胀厚度测试9/strong>将待测电芯(带气袋)放入SWE2110对应通道,开启MISS软件,设置各通道对应的电芯编号和采样频率等参数,软件自动读取电芯厚度、厚度变化量、测试温度、电流、电压、容量等数据、/p>
2. 结果分析
2.1 电芯总体积膨胀的结果分枏/strong>
将同批次电芯A置于原位产气体积监控仪(GVM2200)内,设置循环控温系统的温度?5℃,并实时监测电芯A在化成过程中的体积变化,结果如图2所示。整个化成过程可分为四个阶段:首先是发生在负极端的低电压产气阶段,主要产生乙烯(C₂H₄)、乙烷(C₂H₆)等气体。第二阶段为气体生成与消耗并存的阶段,因此产气曲线的斜率相较第一阶段有所变缓。J.R. Dahn等人[4]认为此时生成的部分C₂H₄会发生聚合反应生成聚乙烯,并导致产气的总体积增量有所减缓。第三阶段为高电压产气阶段,主要发生在正极端,并大量产生二氧化碳(CO₂)等气体,此时产气曲线的斜率与第一阶段相当,并?.647~3.671 V时达到最大值~365 μL。第四阶段为化成末期,随着充电的继续进行,电芯整体的膨胀体积不再继续上升,并呈现轻微的下降趋势,这主要是由于正、负极表面已生成较为稳定的SEI膜,不再继续产生气体,但是部分C₂H₄仍会继续发生聚合反应或与CO₂发生消耗反库sup>[4],致使化成后期电芯的总体积呈现轻微下降趋势(~16 μL)。值得注意的是,该设备检测的电芯体积膨胀一方面包括产气导致的软膨胀,另一方面还包括锂离子嵌入Si/C负极后引起的硬膨胀,因此最终得到的是电芯的总体积变化、/p>
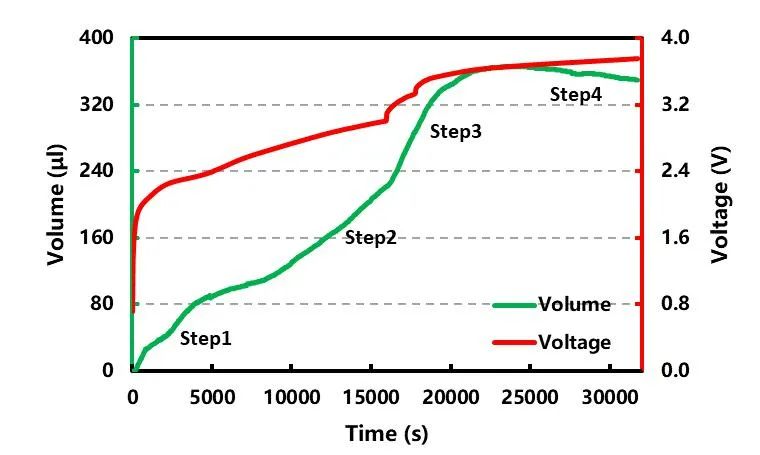
?.电芯充电曲线及体积变化曲纾/span>
2.2 电芯硬膨胀行为的结果分枏/strong>
将同批次平行样电芯B置于原位膨胀分析仪(SWE2110)内,压力模式设置为恒压力模式(压力值恒定为5.0kg),并实时监测电芯B在整个化成过程中的厚度变化,结果如图3所示。在化成的充电前期,电芯B的厚度变化(绿线)并不明显,甚至有细微的降低?0.7μm),这是由于化成初期锂离子主要被用于化成产气(软膨胀),并未嵌入Si/C负极引发硬膨胀,原位膨胀分析仪(SWE2110)在纵向上对电芯施加的预紧力使得化成产生的气体更倾向于横向扩散至电芯侧边的气袋中,并未引起纵向上的厚度变化(化成初期形成的SEI膜厚度小?nm[7],可忽略其对厚度的影响),反而是正极脱锂导致的体积收缩使得相对厚度变化曲线在~3.47 V以下的电压区间内出现了细微的下降。当充电至~3.47 V以上时,大量的锂离子除了用于成膜外,也开始嵌入Si/C负极内并引发硬膨胀,此时相对厚度变化曲线开始出现明显的拐点,并在后续的充电过程中急速增加,直至实验结束。因此,该设备与方法主要检测的是电芯的硬膨胀行为、/p>
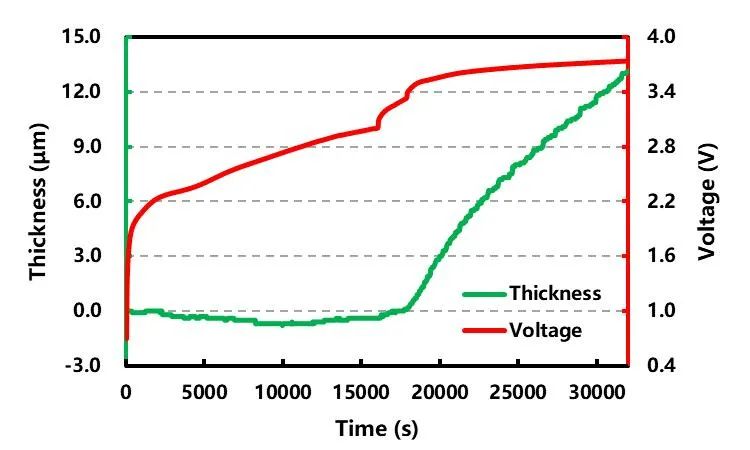
?.电芯充电曲线及厚度膨胀曲线随时间的变化
2.3 电芯?硬膨胀的分禺/strong>
由于测试电流较小,因此我们忽略充电过程中锂离子的浓度梯度对电芯厚度不均匀膨胀的影响。该批次电芯的极片大面尺寸为60mm*45mm,将电芯脱嵌锂的厚度变化量(?测试结果)乘以极片面积,即可求得电芯硬膨胀过程中的体积变化。利用总体积变化量(图2测试结果)减去电芯硬膨胀的体积变化量,便可得到电芯化成过程中的产气体积量,从而实现电芯软膨胀和硬膨胀的有效分离,结果如图4所示。可以看出在~3.47 V之前的电压区间内,软膨胀行为的占比(紫线)一直保持在100%左右(占比略大于100%是由于化成前期电芯不仅没有明显的硬膨胀行为,反而因正极脱锂引起了细微的结构收缩,如2.2部分所述),而在~3.47 V以上的电压区间,锂离子开始有效地嵌入Si/C负极中,此时硬膨胀行为(橙线)开始对电芯的总体积膨胀产生一定的贡献,但是这些贡献最大时(化成末期)也仅占到了总膨胀量的10%左右。因此电芯在整个化成阶段所发生的体积膨胀主要来源于成膜时产气所引发的软膨胀行为(占?0%以上),而嵌锂所引发的硬膨胀行为主要发生在化成的中后期,且所占比例最大时也仅?0%左右、/p>
化成主要是生成稳定SEI膜并伴随产气的过程,电池后期循环过程虽然产气较少,但是整个循环过程中始终伴随着不同程度的产气行为,即电池存在软膨胀过程,特别是在过充、过放、高温等条件下产气也很明显。而电化学膨胀不断反复累积也会产生不可逆形变。因此,在电池循环过程中或者安全测试条件下,采用本文所述方法能够成功区分并定量表征电池的软/硬膨胀,并更深入地分析产气鼓包和电化学膨胀的各自贡献,从而更有针对性地提出电池优化策略、/p>
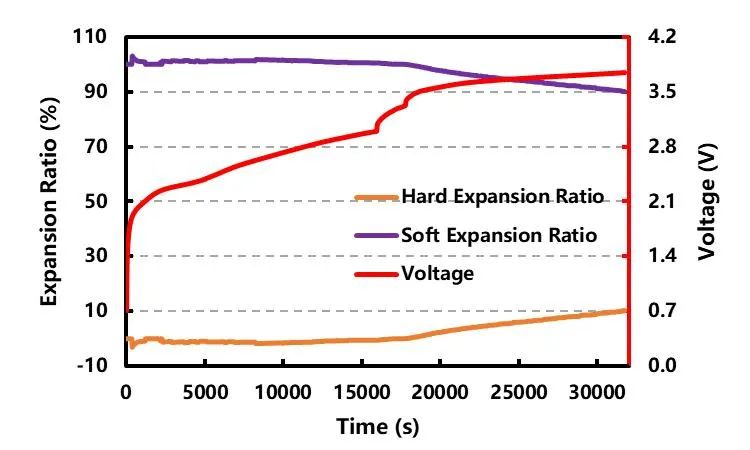
?.电芯化成膨胀和产气变化曲纾/span>
3. 总结
本文采用元能科技(厦门)有限公司的原位体积监控仪(GVM)并配合原位膨胀分析仪(SWE),对NCM/SiC体系电芯化成阶段的软/硬膨胀行为进行了定量的表征与分离,发现在整个化成阶段,电芯所发生的总体积膨胀主要来源于成膜时产气所引发的软膨胀行为(占?0%以上),而嵌锂所引发的硬膨胀行为主要发生在化成的中后期,且所占比例最大时也仅?0%左右。该原位定量分离方法有助于相关技术人员对硅基负极材料的膨胀行为进行准确深入的研究,并推动硅基负极的商品化进程、/p>
4. 参考文?/strong>
[1] J.R. Dahn, Phase diagram of LixC6. Phys. Rev. B 44 (1991) 9170-9177.
[2] S. Chae, M. Ko, K. Kim, K. Ahn and J. Cho, Confronting issues of the practical implementation of Si anode in high-energy lithium-ion batteries. Joule 1 (2017) 47-60.
[3] J.N. Reimers and J.R. Dahn, Electrochemical and in situ X-ray diffraction studies of lithium intercalation in LixCoO2. J. Electrochem. Soc. 139 (1992) 2091-2097.
[4] J. Self, C.P. Aiken, R. Petibon and J.R. Dahn, Survey of gas expansion in Li-ion NMC pouch cells. J. Electrochem. Soc. 162 (2015) A796-A802.
[5] S.L. Guillot, M.L. Usrey, A. Pena-Hueso, B.M. Kerber, L. Zhou, P. Du and T. Johnson, Reduced gassing in lithium-ion batteries with organosilicon additives. J. Electrochem. Soc. 168 (2021) 030533.
[6] T. Yin, L.L. Zhang, L.Z. Jia, Y. Feng, D. Wang and Z.Q. Dai, Overview of research on float charging for lithium-ion batteries. Energy Storage Sci. Technol. 10 (2021) 310-318.
[7] Y. Wang, J.Q. Kang and Z.X. Tan, Study on SEI reaction of lithium-ion batteries based on the electrochemical degradation model. J. Chem. Eng. Technol. 8 (2018) 137-150.